Multiphase Pump
VREIT Multi-phase Flow Dissolved Air Pump
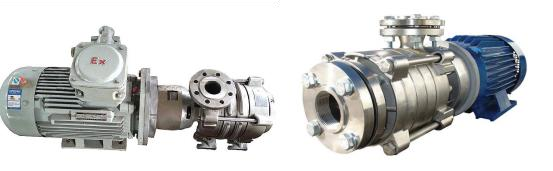
1. Basic Principle
The maximum solubility of gases in water mainly depends on pressure, water temperature, and mixing. The higher the pressure and the lower the water temperature, the greater the saturated solubility of air in water. The more times the mixing and cutting occur, the more dissolved gas can be achieved.
In flotation devices, VREIT Technology's multi-phase flow dissolved air pump is adopted. Gases are directly sucked into the pump inlet pipe by the vacuum generated within the pump itself. The special impeller structure (multi-stage cutting and pressurization) of the VREIT multi-phase flow pump ensures thorough dissolution of gas and liquid phases under high pressure until saturation is reached. When depressurized and released, the dissolved gas emerges in the form of microbubbles dispersed throughout the flotation device. Microbubbles produced through this method can have diameters smaller than 30 microns.
Depending on the properties of gases and liquids, as well as changes in temperature and pressure, the saturated solubility of gases in liquids varies. The performance of the pump remains stable even when there are fluctuations in flow rate and gas volume.
Traditional flotation devices achieve dissolved air through static pressure in a dissolved air tank, which requires a series of related equipment such as air compressors, dissolved air tanks, pumps, control systems, release devices, and valves. Because they cannot ensure that gases are fully saturated in water, large bubbles tend to form upon depressurization and release, affecting the effectiveness of the flotation process. By using multi-phase flow pumps for gas dissolution, not only can most of these devices be eliminated, reducing investment and operational costs, but also due to the fineness and uniform dispersion of the bubbles, the flotation treatment effect is significantly improved.
Compared with jet pump dissolved air systems where gas dissolution occurs in pipelines, the gas dissolution in VREIT multi-phase flow pumps is completed during the multi-stage pressurization process of the pump. The degree of gas dissolution is easier to control, resulting in a more ideal dissolution effect. The efficiency of flotation treatment using VREIT multi-phase flow pumps far surpasses that of jet pump dissolved air systems.
2. Microbubble Generation Principle
Microbubble Production:
- High-speed rotation, breaking bubbles to form stable microbubbles.
- Pressure increase, generating saturated dissolved air water.
- Combination of microbubbles and saturated dissolved air water.
Cavitation Prevention:
- Open impeller design and suitable material selection to prevent cavitation.
- Adaptability to dirty media, resistance to clogging and scaling.
Release Process: Formation of controllable bubble concentration and size distribution.
Sampling for microbubble release (at the pump outlet).
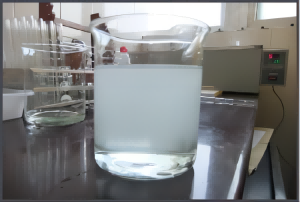
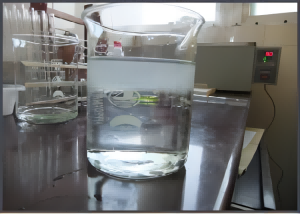
3. Characteristics and Applications of Microbubbles
Flotation: Bubbles consist of dissolved gas released from reduced pressure and microbubbles formed by cutting.
Reaction Enhancement: Improved mass transfer efficiency (by increasing surface area). Conducted under high pressure (blade pressurization + cutting to generate microbubbles).
Degassing: Increased inlet gas flow, proper release port design (nozzle to create localized low pressure, enhancing gas-liquid contact area).
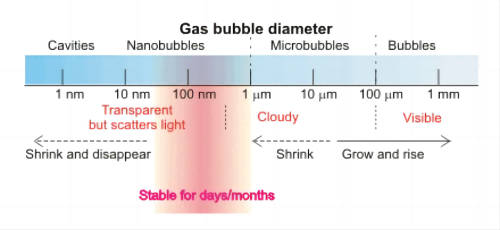

Characteristics of Microbubbles:
- Suitable for various flotation applications.
- Mining (copper mining, solid flotation).
- Deammonification (water treatment, adding air to remove ammonia).
- Ammonium Chloride Regeneration (environmentally friendly etching for circuit boards).
- Ozone Solubilization (water treatment, removal of CODs).
- Acceleration of reaction rates in reactions primarily governed by gas-liquid mass transfer.
- Aquaculture (high density, deep water), oxygenation.
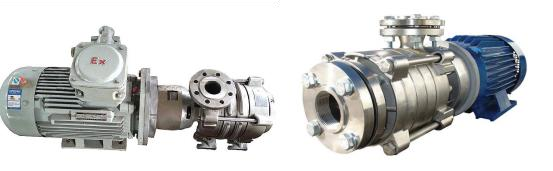
1. Basic Principle
The maximum solubility of gases in water mainly depends on pressure, water temperature, and mixing. The higher the pressure and the lower the water temperature, the greater the saturated solubility of air in water. The more times the mixing and cutting occur, the more dissolved gas can be achieved.
In flotation devices, VREIT Technology's multi-phase flow dissolved air pump is adopted. Gases are directly sucked into the pump inlet pipe by the vacuum generated within the pump itself. The special impeller structure (multi-stage cutting and pressurization) of the VREIT multi-phase flow pump ensures thorough dissolution of gas and liquid phases under high pressure until saturation is reached. When depressurized and released, the dissolved gas emerges in the form of microbubbles dispersed throughout the flotation device. Microbubbles produced through this method can have diameters smaller than 30 microns.
Depending on the properties of gases and liquids, as well as changes in temperature and pressure, the saturated solubility of gases in liquids varies. The performance of the pump remains stable even when there are fluctuations in flow rate and gas volume.
Traditional flotation devices achieve dissolved air through static pressure in a dissolved air tank, which requires a series of related equipment such as air compressors, dissolved air tanks, pumps, control systems, release devices, and valves. Because they cannot ensure that gases are fully saturated in water, large bubbles tend to form upon depressurization and release, affecting the effectiveness of the flotation process. By using multi-phase flow pumps for gas dissolution, not only can most of these devices be eliminated, reducing investment and operational costs, but also due to the fineness and uniform dispersion of the bubbles, the flotation treatment effect is significantly improved.
Compared with jet pump dissolved air systems where gas dissolution occurs in pipelines, the gas dissolution in VREIT multi-phase flow pumps is completed during the multi-stage pressurization process of the pump. The degree of gas dissolution is easier to control, resulting in a more ideal dissolution effect. The efficiency of flotation treatment using VREIT multi-phase flow pumps far surpasses that of jet pump dissolved air systems.
2. Microbubble Generation Principle
Microbubble Production:
- High-speed rotation, breaking bubbles to form stable microbubbles.
- Pressure increase, generating saturated dissolved air water.
- Combination of microbubbles and saturated dissolved air water.
Cavitation Prevention:
- Open impeller design and suitable material selection to prevent cavitation.
- Adaptability to dirty media, resistance to clogging and scaling.
Release Process: Formation of controllable bubble concentration and size distribution.
Sampling for microbubble release (at the pump outlet).
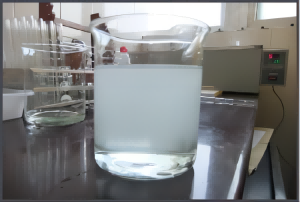
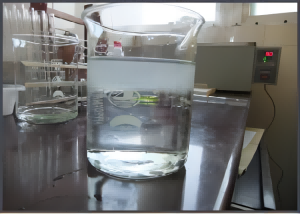
3. Characteristics and Applications of Microbubbles
Flotation: Bubbles consist of dissolved gas released from reduced pressure and microbubbles formed by cutting.
Reaction Enhancement: Improved mass transfer efficiency (by increasing surface area). Conducted under high pressure (blade pressurization + cutting to generate microbubbles).
Degassing: Increased inlet gas flow, proper release port design (nozzle to create localized low pressure, enhancing gas-liquid contact area).
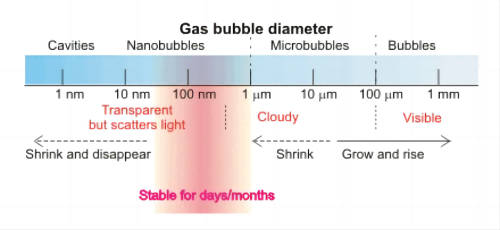

Characteristics of Microbubbles:
- Suitable for various flotation applications.
- Mining (copper mining, solid flotation).
- Deammonification (water treatment, adding air to remove ammonia).
- Ammonium Chloride Regeneration (environmentally friendly etching for circuit boards).
- Ozone Solubilization (water treatment, removal of CODs).
- Acceleration of reaction rates in reactions primarily governed by gas-liquid mass transfer.
- Aquaculture (high density, deep water), oxygenation.
Illustrative Diagram of VREIT Multi-phase Flow Dissolved Air Pump System Structure Shown.
Contact Information: Ye Zilong Phone: +86-133-8667-7776
Email: zilong.ye@vtechcn.com
Contact Information: Wang Jianrong Phone: +86-133-2612-8487
Email: jianrong.wang@vtechcn.com
Products & Solutions
- Metering Module
- Wellhead Monitoring Skid
- Single Well Metering Ski
- Oil-Water Separation Mem
- Slug Catcher
- Vane Type Separator
- Filter cartridge
- GLCC Desander System
- Water Treatment Module
- Micro-Bubble Flotation T
- Hyperbolic hydrocyclone
- Gas dissolution pump
- Mobile Electrocoagulatio
- Mechanical foam eliminat
- Chemical Injection Skid